Blog
Increasing Modernization of Cleveland Warehouse & Distribution Centers Make 3PL Partners a Smart Option
Ever-climbing customer expectations, higher-cost goods, and supply chain snarls have made efficiency in warehousing an imperative. In 2018, there were approximately 8,000 private warehouses in the U.S. Now, there are 22,000, according to the U.S. Bureau of Labor Statistics. As the demand for Cleveland warehouse & distribution services has ballooned, it’s become incumbent upon those operating them to work smarter – not harder. This is where warehouse modernization is taking a front seat.
As an established Cleveland warehouse & distribution center with 30+ years of experience, we know that evolution and modernization is the key to staying competitive. Our core values of prioritizing quality customer service and superior facilities have never waivered. But delivering that requires that we keep a finger on the pulse beat of the latest logistics and warehousing technology – and invest in onboarding them where it makes good sense to do so.
In a U.S. warehouse landscape analysis by Zebra Technologies, a company that makes marking, tracking, and computer technologies, 80 percent of warehouse operational decision-makers say they’ll need to adopt new technology over the next five years to stay competitive. Roughly 85 percent say they’re likely to see an increase in shipping volumes, and thus are going to need to invest in better returns handling – which requires more space, more staff, and more efficient technology.
Constantly-progressing warehousing & distribution tech is one reason third-party logistics (3PL) warehousing partners tend to exceed the performance of other businesses trying to manage it all in-house. Even those with capacity to allocate the time, space, and adequate staffing to these services should also consider how regularly these systems and operations require updates and replacements. You get everything set up – only to find within 3-6 months that some new technology has flipped the script. Suddenly, some new equipment and training is necessary to keep pace.
But when the core operations of a company ARE warehousing and distribution, clients of those firms get the benefit of that expertise in identifying problems faster and devoting more time and resources to ensuring all practices, technology, and training is up-to-date.

Fast-Tracked Digital Updates in Cleveland Warehouse & Distribution Operations
Warehousing – and supply chains overall – have always been dynamic. In these worlds, adaptability is survival.
These past few years though, what’s been unique is the frenetic pace at which change has been happening. The pandemic revealed how complex and fragile some supply chains are, and the need to invest in competitive resilience. Part of that includes ensuring the warehousing and distribution services you’re using are operating at prime transparency and efficiency.
Among the warehouse tech solutions on the horizon with significant potential:
- Data and visibility applications. Historically, most supply chains were sort of a simple, top-down business model. That is, the order’s origin, “in-stock” status, and estimated shipping time were the only bits of information readily available. But that’s not good enough anymore. There is a baseline expectation that warehouses have the sort of visibility that will allow for live tracking of products and goods in the warehouse and through the distribution process. These include things like Bluetooth tags, camera sensors, and radio-frequency identification (RFID). It’s smart because greater transparency in the supply chain allows issues to be quickly spotted and effectively addressed. New technologies allowing for improved warehouse visibility are being rolled out practically every year. That’s not to say they need to be updated annually, but warehouses need to ensure the software they’re using is reliable and allows their clients to stay competitive.
- Improved track & trace tech. These applications are already utilized by high-volume industries, such as apparel. It’s gotten to the point where a postage stamp-sized tracker can be used to track products from start to finish – and at any location within a warehouse. We’re going to see industries like produce, pharmaceuticals, and metals (those relying on strict temperature and environmental controls).
- AI technology. Artificial intelligence (AI) is fast becoming more complex, advanced, and impressive. It has such a broad range of possible applications – but many warehouses are somewhat hesitant. But there are some programs that use AI that can be extremely helpful with visibility deficits – particularly flagging issues and inefficiencies in real time and formulating solutions.
If you have questions about the type of warehousing and distribution technology we utilize and how we can use it to meet your operational needs, give us a call or send an email!
For information on Warehousing, Inventory Management, Fulfillment, Distribution, and Trucking Services in Cleveland, Contact On Time Delivery & Warehouse by calling (440) 826-4630 or send us an email.
Additional Resources:
Bringing Warehouses Of The Past Into The Future, Nov. 11, 2022, By Lior Elazary, Forbes Business Council, Forbes Magazine
More Blog Entries:
Perks of Using a 3PL Cleveland Fulfillment Center to Move Your Goods, Jan. 27, 2022, Cleveland Warehousing & Distribution Blog
- Categorized: Company News
- Tagged: Cleveland third-party logistics, Cleveland warehousing, Northeast Ohio 3PL, Northeast Ohio warehousing, Ohio 3pl
Perks of Using a 3PL Cleveland Fulfillment Center to Move Your Goods
Virtually any company that relies on e-commerce can benefit from 3PL fulfillment services. Some of the most popular Cleveland fulfillment center services that we offer at On Time Delivery & Warehouse are bundling, warehousing, picking and packing, kitting, labeling, product coding & repacking, shipping (including same day shipping), inventory management, customs & import guidance, and logistics solutions.
Outsourced fulfillment services make the most sense for companies that:
- Lack internal resources to ensure consistently robust warehousing capabilities.
- Have minimal inventory management potential.
- Don’t have enough time or staff to dedicate to shipping and distribution.
According to analysis by Grand View Research, the market value of global e-commerce fulfillment services is estimated to have a compound annual growth rate of nearly 10 percent between now and 2030. That means it’s likely no matter what your field, a growing number of competitors will begin more fully appreciating the benefits of partnering with a third-party Cleveland fulfillment center to provide key services.
How Do Cleveland Fulfillment Center Partnerships Work?
When it comes to logistics and managing supply chains, even smaller operations may have complexities that can impact how fast orders are delivered to the end customer – and in what condition. There are often many puzzle pieces that need to fit together just right to ensure the desired outcome and timeline.
At the center of that puzzle is often the fulfillment center.
Fulfillment center operators can wear many hats, but they’re typically third parties responsible for processing and shipping products that have been ordered/purchased. These facilities are often large and centrally-located to ensure faster shipping times at lower costs. They can serve both business-to-consumer or business-to-business operations.
While the terms “fulfillment center” and “warehouse” are sometimes used interchangeably, there are some differences. Most fulfillment centers are also warehouses or linked with warehousing services. However, not all warehouses are fulfillment centers. Whereas warehouses are places to store goods, materials, and products, the fulfillment center is responsible for meeting customer demands through efficient processing and shipping.
Half a Dozen Benefits of Quality Fulfillment Services
Outsourcing your distribution and fulfillment services can potentially reduce shipping costs by anywhere between 15 and 35 percent. That’s usually the most compelling draw for most companies. But there are other upsides too – some of which also contribute to the bottom line boost.
At the top of our list:
- Avoiding a brick-and-mortar investment. Although this trend started pre-2020, the pandemic threw into stark relief the fact that many operations are using more physical space than they need. Warehousing, fulfillment, and distribution services often require a lot of space – which can cost a lot of money, particularly if you are renting/paying taxes on/insuring/managing/equipping/staffing your own facility. It usually only makes sense for very large companies or those that consistently move huge volumes to manage their own fulfillment and distribution operations. For others, third-party logistics fulfillment centers are the ideal solution.
- Faster order processing. When you work with a dedicated fulfillment center, orders can typically ship faster than you’d be able to manage on your own. This is not only thanks to the central location and value-added services, but also the superior logistics team, which ensures a more efficient supply chain.
- Better shipping experiences. Of course, your customers want to receive their orders intact and on time – every time. But increasingly, they also want to be able to track their order in real time. They want to know right away if there’s a delay – or if it will be there sooner than expected. Proper packaging is important too, as is a fast turnaround time. A third-party fulfillment operation can provide these things easier than a firm that isn’t dedicated to full time warehousing and distribution.
- Greater scalability options. If you’re going to put the time, energy, and resources into establishing your own fulfillment center, it can be difficult to scale down – or up – as needed without losing money. If you get a sudden lull or surge in orders, a 3PL fulfillment center can accommodate those fluctuations without significant losses.
- Improved logistics. The complexities of inbound and outbound logistics can be overwhelming if that’s not your core operation. When you contract with a 3PL for fulfillment services, you get the benefit of experts with decades of experience in services like order processing, inventory management, picking and packing, warehousing, distribution, and more. When you entrust the logistics leg of your operation to logistics experts, you not only provide your customers with better service, you’re also better able to respond to supply chain volatility.
- Value-added services tailored to your needs. There is no one-size-fits-all business or organization, and there’s no one-size-fits-all package of warehousing and distribution services that are going to work for everyone. A well-managed fulfillment center can often provide customized value-added services so you get exactly what you need – and aren’t paying for things you don’t.

Choosing an Ohio Distribution & Fulfillment Service Provider
When you’re looking to contract with a Cleveland fulfillment center, some important considerations include:
- Which services are provided? Most fulfillment service providers have some basic warehousing and shipping packages. But can the facility and their staff actually handle all the receiving, storing, picking, packing, labeling, kitting and other needs your operations and customers require?
- What are their price points? The financial incentives are what typically draw customers to seek fulfillment center partners. But the key to get the most of your partnership is to carefully assess what you’re getting for what you’re paying. If certain services cost more than their competitors, is there a good reason for that? Ask too about whether they have shipping specialties for certain service areas, volumes, types of goods, etc.
- How central is their location? Ideally, the fulfillment center you choose will be fairly close to your customers. The less distance they need to cover to complete your deliveries, the faster your orders can be fulfilled and the less it will cost you.
- How is their responsiveness? Customer service is key in fulfillment. If something goes sideways or there is any type of disruption in your distribution process, you need to be able to reach someone who can help you remediate the issue right away. Transparency is also an element of this that’s worth inquiring about.
If you have questions about our Northeast Ohio fulfillment and distribution center, contact us for more information and a quote.
For information on Warehousing, Inventory Management, Fulfillment, Distribution, and Trucking Services in Cleveland, Contact On Time Delivery & Warehouse by calling (440) 826-4630 or send us an email.
Additional Resources:
Warehousing Giants Are Consolidating in a Shifting Real-Estate Market, June 13, 2022, By Liz Young, The Wall Street Journal
More Blog Entries:
Perks of Cleveland Public Warehousing, Nov. 23, 2022, Ohio Warehousing Blog
Reducing Cleveland Trucking Turnaround Times, Dock Delays, and Detention
Ohio companies looking to prioritize supply chain efficiency in 2023 would do well to aim at least part of their focus on reducing Cleveland trucking turnaround times, dock delays, and detention issues.
The U.S. port surge that threw international supply chains out of whack for the better part of three years during the pandemic is finally beginning to subside. However, analysts with the Journal of Commerce say that marine terminals (which effectively became container storage facilities when overwhelmed by cargo surge) aren’t prepared for another wave – and that’s bound to happen again at some point.
As Cleveland trucking experts, we recognize that while improved port procedures are central to fixing problems stemming from cargo surges, it’s also important for logistics, delivery, and warehouse operators to prioritize streamlining their own practices. This is especially true given that last year, companies looking to avoid ongoing supply chain bottlenecks opted to ship tens of thousands of containers via truck rather than rail – despite higher costs – because it was largely deemed more reliable. Rail industry setbacks like shortages in labor, equipment, and warehouse space aren’t going away anytime soon. That means we’ll continue to see a growing demand for trucking capacity – and lower turnaround times will be more pivotal than ever.
What Exactly Is Cleveland Trucking Turnaround?
Trucking turnaround time is one of the main performance indicators used to measure efficiency of port logistics and drayage services (transport of freight from an ocean port to a destination). It’s generally defined as the window of time a trucker spends at a terminal, port, or customer pickup area – from gate entry to gate exit. The pickup/drop-off process involves loading, unloading, inspecting, and completing proper documentation.
All this can be impacted by dock delays (particularly when there’s a cargo surge). But optimal trucking turnaround times aren’t solely the responsibility of port service workers. Trucking companies must prioritize efficiency at all junctures – not only at ocean ports, but on the road, at inland warehouses, while navigating distribution centers, etc. This is why it’s key to work with a Cleveland trucking operator that knows what they’re doing, recognizes their role in meeting your deadlines, and takes its professional relationships and responsibilities seriously.
While it’s true we’re seeing an ebb in cargo surge at the moment, no operation that relies on efficient supply chains can afford to presume it won’t happen again – perhaps sooner than later. What’s more, we’re unlikely anytime soon to see a lull in other factors impacting delays and detention – including rising fuel costs, labor shortages, and a boom in online spending. Demand for trucking capacity is only going to increase.
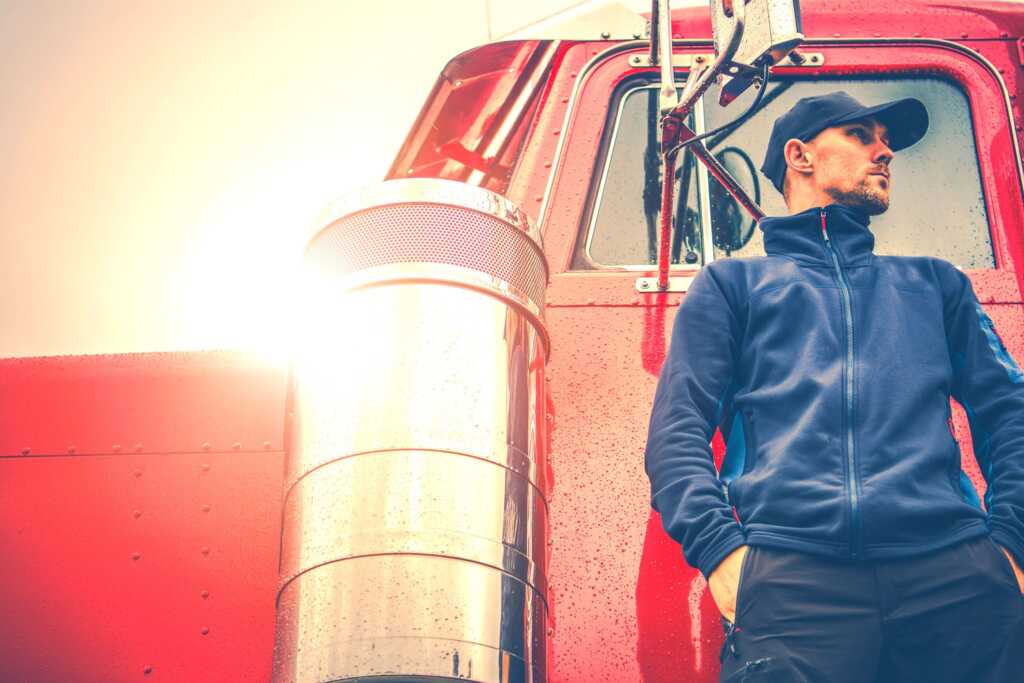
How Detention Impacts Trucking Turnaround Times – and Bottom Lines
Detention delays occur when a trucker is held up by terms or circumstances outside their control – usually due to inefficiencies at the dock, warehouse, customer facility, or distribution center.
In a recent report by the American Transportation Research Institute, truck detention and delays at customer facilities ranked in the top 5 industry concerns for U.S. truck drivers. Nearly one-third of drivers reported increases in detention time delays of 6 hours or more over the last 5 years. The most significant delays are reported by those in refrigerated trailers, followed by those operating bulk/food trucks, tanker/hazmat vehicles, dry vans, and finally flatbed trucks. Such delays are also more common with full truckload shipments compared to less-than-truckload (LTL) shipments.
These issues can be exacerbated when delays start running up against hours of service regulations – the maximum amount of hours truckers are allowed to work by federal law. Driver compensation for excess detention can range anywhere from $10/hour to $100/hour (most in the $50+ hour range). The longer truckers are unnecessarily detained at a port or customer site, the worse their overall turnaround times are going to be. Perhaps even more concerning: It’s also associated with a heightened risk of truck crashes. The longer hours a trucker works, the more fatigued they are, and the greater their risk of an accident.
The U.S. Department of Transportation reports detention nationally costs somewhere in the ballpark of $1.1 billion to $1.3 billion each year.
As for the root of this problem, it’s varied. Many drivers point to apathetic or untrained dock employees, double-booked docks, lack of adequate dock space, and issues with paperwork. Lack of trucker parking is also a problem (something even the White House has acknowledged is an issue). Truckers who aren’t allowed to park on site must wait outside the customer facility – sometimes miles away, in areas that aren’t exactly equipped for it. This can further exacerbate delays as well as compromise driver safety.
Improved scheduling and planning, longer hours, more employees/space/equipment, and better employee training were all cited as possible solutions to shortening dock delays, excessive detention, and truck turnaround times.
Enhancing inbound and outbound logistics strategies to maintain reasonable trucking turnaround times is going to prove increasingly important to companies hoping to retain their competitive edge.
Companies that partner with a third-party logistics company may see faster – and more tangible – results on this front.
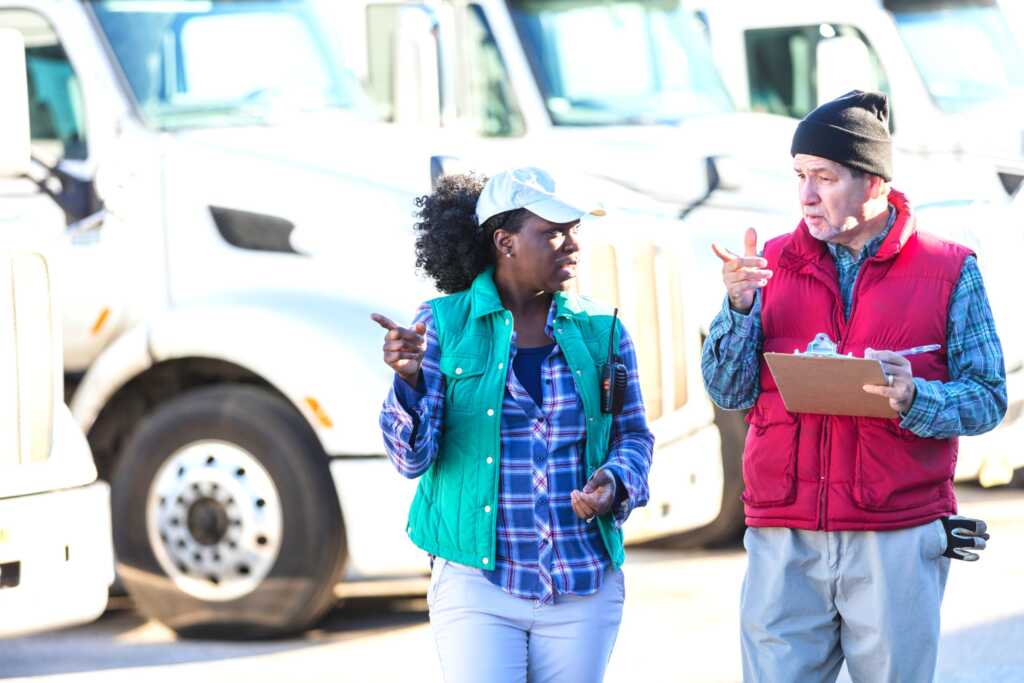
How Trusted Ohio Truck Firms Can Reduce Turnaround Times
Ohio trucking companies generally aren’t in control of things like erratic consumer demand, international cargo surges, or lack of trucker parking. But that doesn’t mean they’re powerless.
Established transportation companies know that when these issues can’t be avoided, there are still ways to prepare and minimize the potential impact for customers.
Such measures include:
- Upgraded and well-maintained equipment. Older trucks and monitoring equipment will be vulnerable to failures, glitches, and breakdowns – which can further exacerbate delays and lengthen Cleveland trucking turnaround times. It’s important that not only is the fleet itself in great shape, but the technology used for transportation GPS and supply chain tracking and forecasting is also up-to-date and keeps pace with ever-evolving logistics insights. Transparency technology can also help set clear expectations and make adjustments as necessary if it seems delays are likely.
- Smart balance of trucks-to-drivers. This isn’t an exact science, but companies tend to have more drivers than trucks. However, that means any shortage of functioning trucks that can’t be promptly addressed will lead to fewer shipments, higher costs, and longer turnaround times. Trucking companies that keep their fleets in good working order as well as maintain a good truck-to-driver ratio will generally see fewer detention issues.
- Streamlined administration communication. Communication is central to supply chain efficiency. When you work with a 3PL trucking company with established relationships with local and regional partners, you get the benefit of those longstanding, well-oiled workflow and communication processes.
- Investment in experienced, well-trained drivers. Truck driving is often a more skilled profession than some people might presume. It’s not just about being safe behind the wheel. It’s about being effective with organization, time management, communication, and preparation. When delays occur, truckers who are prepared, properly trained, polite, and persistent are often rewarded with lower turnaround times.
If you have questions about how working with a dedicated 3PL trucking company in Northeast Ohio can help you reduce your trucking turnaround times and detention costs, we can help.
For information on Ohio Trucking Services in Cleveland and throughout Northeast Ohio, Contact On Time Delivery & Warehouse by calling (440) 826-4630 or send us an email.
Additional Resources:
Driver Detention Impacts on Safety and Productivity, September 2019, American Transportation Research Institute
Reducing external container trucks’ turnaround time in ports: A data-driven approach under truck appointment systems, December 2022, Computers & Electrical Engineering
More Blog Entries:
Why Companies are Increasingly Turning to Cleveland Dedicated Trucking, Nov. 28, 2022, Ohio Truck Company Blog
- Categorized: Company News
Cleveland Freight Consolidation: Lower Costs, Greener Commerce, Happier Clients
Surging e-commerce demands are the new normal in trade – both domestically and globally. Staying afloat means keeping costs reasonable, prioritizing customer satisfaction, and implementing greener supply chain practices for sustainability. One way to check all three boxes is with Cleveland freight consolidation.
Freight consolidation is a practice whereby shippers combine multiple less-than-truckload (LTL) shipments all destined for the same geographical end point. If a single shipper only uses two-thirds of a trailer, they’re still going to pay for the entire space – unless the freight can be efficiently consolidated with orders from other customers headed in the same direction. In that case, they can split the cost of a single trailer, paying only for the percentage of space they’re actually using.
When freight is consolidated, shippers can make the most of every trip. Fewer large truck trips is not only cheaper, it also means less gas and roadway wear-and-tear, which is a net positive for the environment.
For end customers, freight consolidation has two major benefits: Shorter lead time and lower shipping costs. Faster order fulfillment is possible when companies can afford to ship smaller orders right away, as opposed to spacing them out to allow for buildup of a volume that will justify the expense of an entire truckload.
More than simply an added bonus, these savings can be a make-or-break factor when weighed against the economic strain so many firms are currently facing, such as ongoing labor shortages, port congestion, tight transportation capacity, record-high warehouse pricing, and the overall rising cost of raw materials and packaging.
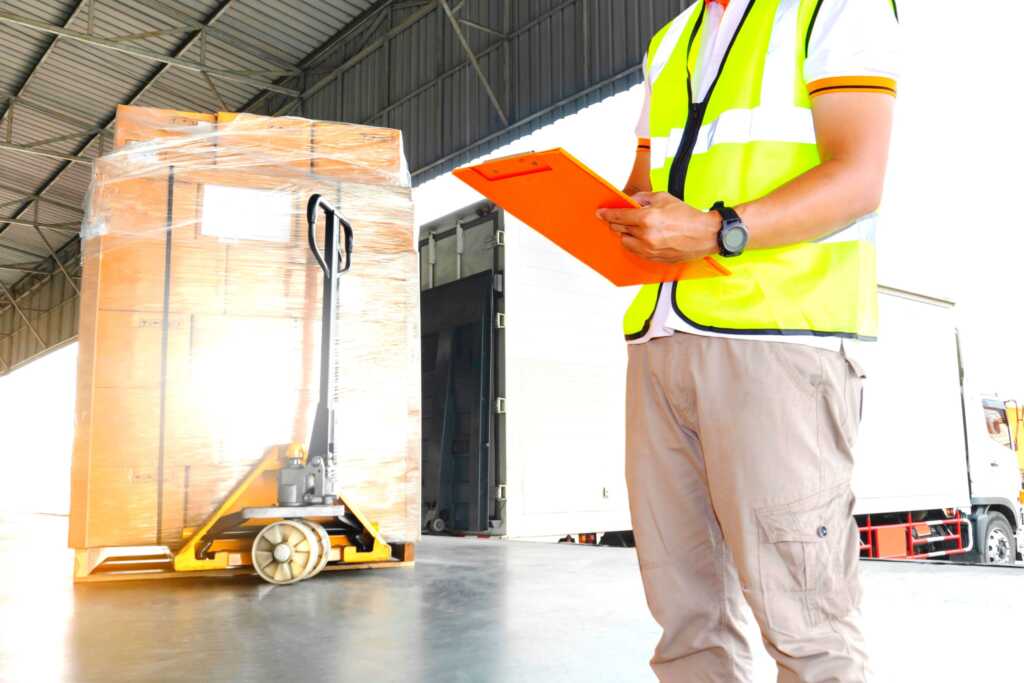
Third-Party Logistics’ Role in Cleveland Freight Consolidation Strategies
The many benefits of Cleveland freight consolidation for import and export freight are well-established. The biggest implementation challenge for most companies is effective coordination of all the moving parts needed. This is where a third-party logistics (3PL) company can prove indispensable.
A 3PL has not only the insight on the most efficient routes and fleets, they can connect clients from all over with similar goals – in the region, on the route, at a central consolidation/distribution center, or at similar retail destinations.
Clients benefit from the long-standing working relationships third-party logistics operators have forged with strategically-situated warehouses, distribution centers, shippers, and retailers. This allows for improved communication and flexibility, which ultimately translates to:
- Quicker delivery times
- Improved order visibility
- Simple pricing
- Better level of service
- Reduced loading dock congestion (fewer trucks means less processing time and faster in-and-out)
- Minimized handling (fewer touches mean less product damage risk, particularly when working with an experienced 3PL)
- Boosted sustainability
- More control over production schedules and due dates
Don’t solely take our word for it: In a recent analysis published by the U.S. Department of Transportation on the impact of freight consolidation and truck sharing. Study authors looked at several algorithms designed to aid online freight marketplaces in identifying efficient consolidation strategies, as well as route optimization and consolidation in a handful of mid-sized cities.
Ultimately, the cost savings potential of freight consolidation just in these few markets showed:
- Same delivery volumes achieved with only 67 percent of current truck usage.
- Operational costs reduced by 23 percent.
- Mileage expenditures slashed by 17 percent.
While the study didn’t specifically zoom in on how this process minimized environmental impact, that benefit is inherent anytime the number of trips and truckloads goes down.
For information on our Cleveland freight consolidation services, contact On Time Delivery & Warehouse by calling (440) 826-4630 or send us an email.
Additional Resources:
Study the Impacts of Freight Consolidation and Truck Sharing on Freight Mobility, April 1, 2019, U.S. Department of Transportation
More Blog Entries:
Cleveland Transloading Service Benefits, Oct. 15, 2022, Northeast Ohio CFS Freight Blog
- Categorized: Warehousing
7 Upsides to Contracting With a Cleveland Domestic Freight Forwarding Company
Cleveland domestic freight forwarding is an invaluable supply chain service for businesses of all sizes that seek to meet customer demand, expand market reach, and still keep the internal focus on core competencies.
A freight forwarder is basically a third-party logistics business that helps other companies arrange the import and/or export of cargo. In so doing, they often provide critical supply chain management services, such as inland transportation, warehouse storage, document preparation, consolidation/deconsolidation, and customs clearance. Freight forwarding can be done internationally or domestically, depending on where your goods are ultimately ending up.
The particulars can get complicated, but the general idea is that when your business needs goods moved from A to B, you can hire a 3PL freight forwarder, which then maps out the most efficient, cost-effective chain of supply for your operation Freight forwarders can use either their own resources (trucks, drivers, warehouse space, labor, etc.) OR by tap into shipping partner connections.
At On Time Delivery & Warehouse, our experienced freight forwarding team of Cleveland domestic freight handlers assists with loading and unloading cargo and overseeing quality control with meticulous review of goods unloaded/loaded from one vehicle or carrier to the next. We also provide clients with trucking and warehousing services.
According to the U.S. Bureau of Transportation Statistics, more than 55 million tons of freight – some $54 billion worth – is moved daily in the U.S. transportation system. The largest percentage of shipped goods – 75 percent by both weight and dollar value – is moved within relatively short distances, 250 miles or less. Trucks are the transport mode that moves the most domestically, particularly for shipments moved 1,000-miles-or-less. Domestic freight transport can also involve rail, air freight, or a combination intermodal supply chain resources.
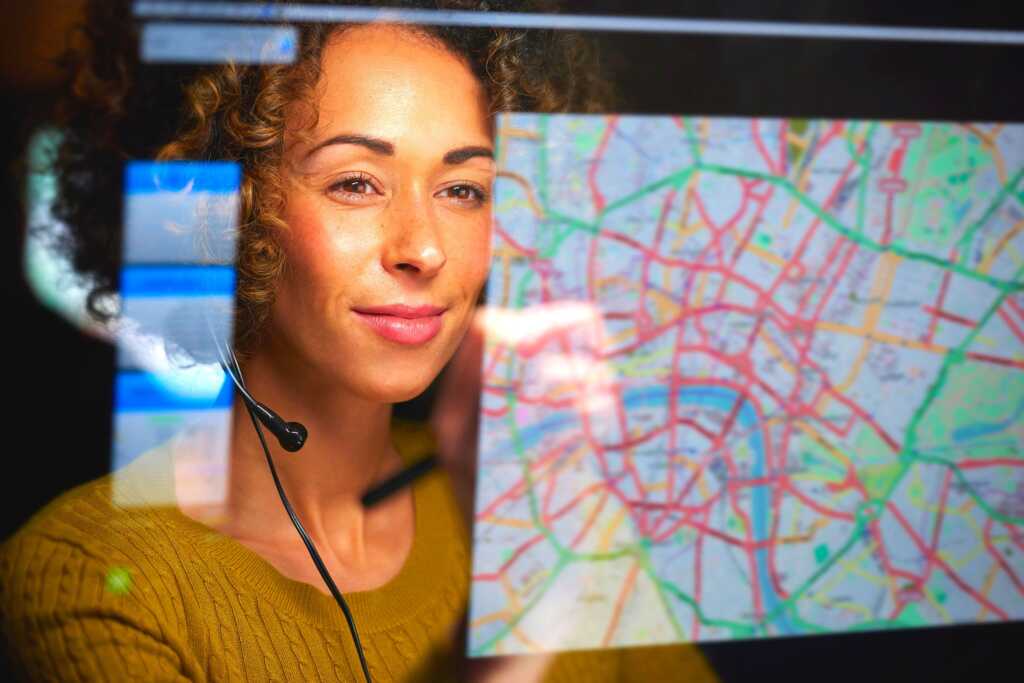
Top Advantages of Having a Cleveland Domestic Freight Forwarding Partner
For companies that routinely ship high volumes of products, the many advantages of hiring a Cleveland freight forwarding:
- Competitive pricing based on needed services. Ohio domestic freight forwarding companies can leverage volume to reduce your costs. As intermediaries, freight forwarders have forged reliable working relationships with multiple shippers. This allows them access to more routes, specialty services, and pricing options, and then quickly strike shipment deals on their behalf. Freight forwarders can also sometimes finagle lower shipping prices through cargo consolidation among numerous customers. A single container can carry multiple customers’ cargo, and they all collectively pay less for it.
- Greater shipping flexibility. Shipping domestically and globally is time-consuming, costly, labor-intensive – and at constant risk of last-minute, unexpected changes. Ports experience bottlenecks. Crashes happen on major highways. Blizzards blow through the entire Northern half of the country. Supply chains are always going to be at risk of setbacks like this. Freight forwarding companies can’t shield you entirely, but they can forecast problems on the horizon, identify issues as soon as they crop up, and quickly connect you to alternatives that will minimize the financial impact.
- Environmentally safer shipping. Environmentally-conscious companies often opt for freight forwarding to manage their shipping needs. Freight forwarders use space-efficient packing methods, prioritize making the most of less-than-truckload orders, ensure fleets are well-maintained, and aim for route optimization with every single trip – all of which can help reduce the overall number of trips to be made and improve fuel efficiency.
- Experience and accountability. Anytime goods are being transported, there’s always the risk something could go wrong. In those scenarios, having a freight forwarding partner with extensive experience and industry knowledge can make a huge difference in maximizing your time and resources and minimizing losses. They are going to be able to identify and secure alternative arrangements. Freight forwarding customers also have a clear line of accountability when things do go sideways.
- Real time cargo tracking and transparency. Effective use of cargo tracking technology is key in helping companies – and their customers – manage price predictions, delivery expectations, and operational goals. You need to know “how long will it take for my goods to get there.” Chances are, your freight forwarder is already using advanced tracking technology to give their clients this edge.
- Accurate documentation. Documentation is a huge issue for companies shipping freight internationally, but it’s still relevant for Ohio domestic freight forwarding companies. Interstate shipments still need to be accompanied with appropriate documentation, such as the bill of lading (the contract between you and the freight carrier), the freight bill, packing list, and proof of delivery (not required, but beneficial). Any domestic HAZMAT shipments will require additional documentation. Making sure all your paperwork is accurate and in order helps to ensure your domestic freight will arrive intact, on time, every time.
- Less hassle. You have an entire business to run. Working with a Cleveland domestic freight forwarding company allows you to keep your focus on what you do best, while we focus on what we do best.
If you have questions about domestic freight forwarding services in Cleveland, our dedicated third-party logistics team at On Time Delivery & Warehouse is here with answers.
For information on Northeast Ohio freight forwarding and freight handling services, Contact On Time Delivery & Warehouse by calling (440) 826-4630 or send us an email.
Additional Resources:
Freight Facts and Figures, Bureau of Transportation Statistics
Moving Goods in the United States, U.S. Department of Transportation, Bureau of Transportation Statistics
More Blog Entries:
Why Companies are Increasingly Turning to Cleveland Dedicated Trucking, Nov. 28, 2022, Cleveland Trucking & Warehousing Blog
Why Companies are Increasingly Turning to Cleveland Dedicated Trucking
Dedicated trucking services can provide stability, efficiency, and cost savings to companies with consistent truckloads in relatively predictable freight lanes for fixed rates. Sometimes referred to as dedicated trucking, dedicated freight, dedicated transportation, or primary freight, these long-term contracts are basically the opposite of spot rate trucking (short-term, transactional freight pricing that reflects the real-time balance). Cleveland dedicated trucking contracts are ideal for established companies with fairly dependable demand.
According to the American Transportation Research Institute, the trucking industry as a whole hauls more than 10 billion tons of freight annually, comprising nearly 75 percent of the total domestic tonnage in the country. There are roughly 4 million registered tractor trailers in the U.S., with those based in the Midwest accounting for more than 40 percent.
Truckload markets are notoriously volatile, swinging from tight carrier capacity and high rates in one quarter to one where per-rate-mile and freight rate increases are scarce. Entering into a longer-term dedicated trucking contract can provide some much-needed cost dependability, as it locks in competitive rates and available trucks for the duration of the contract – typically 3-5 years.
On Time Delivery & Warehouse offers Cleveland dedicated trucking to Northeast Ohio customers seeking greater regularity in their supply chain.
Primary Benefits of Cleveland Dedicated Trucking
There are a number of reasons dedicated transportation has spiked in popularity. Among them:
- Reduced fleet management responsibilities. When you sign a contract for dedicated trucking with a third-party logistics firm, you get lots of the same perks as a private fleet – without the hassle and cost. Instead, it’s the 3PL trucking company that shoulders the work of acquiring and maintaining trucks, hiring and training drivers and support staff, and keeping pace with safety and statutory requirements.
- Stable pricing. Transportation rates are seemingly always in flux, thanks to unpredictable gas prices, labor shortages, updated safety rules, etc. For shippers, this often means coping with sudden cost spikes – on top of erratic trucking capacity. But if a shipper has a dedicated trucking delivery contract, their vulnerability to freight market fluctuations is substantially reduced. Furthermore, dedicated trucking reduces idle truck time, which also keeps costs in check.
- Dependable delivery times. On Time Delivery & Warehouse prides itself on ensuring deliveries arrive intact, on time, every time. Customers with dedicated delivery trucking contracts have even greater assurances because their inbound/outbound shipments are already clearly mapped out. That allows for greater consistency with pickup and delivery times.
- Guaranteed freight capacity. Dedicated transportation requires an established network and consistent routes. This translates to reliable services for shippers, who can depend on that guaranteed freight capacity as outlined in the contract.
- Minimized liability. When customers opt for dedicated trucking services, routes are arranged for goods and products to move from Point A to Point B without other stops along the way (as there might be with less-than-truckload or spot rate deliveries). Fewer stops means less risk of delays and accidents, which in turn reduces shipper liability.
- Greater customer satisfaction. When it comes to deliveries, speed and reliability are at the top of most customers’ priority lists. Dedicated trucking contracts help ensure you’re meeting – or exceeding – their expectations, which in turn boosts not only your bottom line but your reputation.
Cleveland dedicated trucking services hinge heavily on mutual trust. The carrier must commit to a certain amount of driver and trucking capacity, while the shipper commits to a certain amount of regular freight. If you’re considering a dedicated transportation arrangement, it’s important to carefully vet the reputation of the 3PL/carrier. Trucking is a tough business and supply chains are always changing. When a company has been in business for decades, it means they’ve gained customer confidence through successful navigation of challenge after challenge, year after year.
For information on Northeast Ohio Trucking Services in Cleveland, Contact On Time Delivery & Warehouse by calling (440) 826-4630 or send us an email.
Additional Resources:
An Analysis of the Operational Costs of Trucking: 2022 Update, August 2022, American Transportation Research Institute
More Blog Entries:
Cleveland Transloading Service Benefits, Oct. 15, 2022, Northeast Ohio Dedicated Trucking Services Blog
Perks of Cleveland Public Warehousing
Cleveland public warehousing and distribution demand is at an all-time high.
The Journal of Commerce attributes overall warehousing demand in part to the second-quarter surge in imports that led to higher inventories. From this emerged a greater need for logistics and distribution space – particularly in the Midwest and other inland hubs. Beyond that, shifting distribution patterns that emerged during the pandemic have opened new corridors, driving higher demand in markets that used to be considered secondary. Plus, warehouses in major supply chain hubs start brimming to peak capacity, it’s the adjacent smaller markets that absorb the overflow.
Growth in this sector may mean organizations have fewer Ohio warehousing options to choose from, but it’s still important to carefully consider whether the facilities you’re eyeing can check all those “must have” boxes. For many small-to-midsized businesses, that has increasingly meant opting for Cleveland public warehousing vs. private warehousing.
What is the Difference Between Public & Private Warehousing?
As an industry sector, warehousing has evolved far beyond the times of a simple storage space. Today, warehousing is widely recognized as a central service relied upon by industries of all kinds – from consumer goods to manufacturing to retail. As an industry sector, it’s evolved far beyond
Large corporations with high volume product turnover often opt for private warehousing, in which they own or rent warehousing space that is internally operated and overseen. But for any organizations lacking the infrastructure, expertise, and capacity to take on these responsibilities, private warehousing is an attractive alternative that offers affordability, flexibility, efficiency, and convenience.
Put simply, a public warehouse is usually a large facility owned/operated by a third-party logistics (3PL) provider that offers storage space, inventory management, product fulfillment, kitting and packaging, and distribution services to many different businesses.
Cleveland public warehousing costs are typically based per-square-foot, with add-on services available depending on the customer’s needs. Some warehouses require minimum average order volume and/or higher storage rates for slower-moving shipments.
Outsourcing Northeast Ohio warehouse functions is smart when companies:
- Are just starting out and/or are relatively small.
- Have unpredictable inventory cycles.
- Need specialized storage and distribution.
- Lack the investment capital, bandwidth, time, or desire to invest in opening, staffing, and maintaining a warehouse in-house.
It’s important if you’re in the market for public warehouse space to make sure your top picks are not only cost-effective but centrally-located with scalability potential and a great reputation.
Key Benefits of Cleveland Public Warehousing
Among the primary advantages of public warehousing:
- Low investment. Private warehouses are very expensive. There’s procuring and/or building the structure itself. Then there’s maintaining the building, covering all operational expenses, recruiting/training/supervising workers, investing in technology to boost transparency and efficiency, and paying all tax-related expenses. With public warehouses, it’s essentially turnkey.
- Experience and expertise. Labor is usually the biggest expense for most businesses – especially if you want good people. Public warehousing allows companies to avoid direct management of that labor, while still trusting that the workers are knowledgeable and skilled.
- Specialty storage. If you require Ohio warehousing facilities with certain specialty requirements such as FDA registration or hazardous material capacity, it’s often easier to onboard with a public warehouse rather than start from scratch on your own. Not every public warehouse will be capable of fulfilling every specialty requirement, but they can usually refer you to one nearby that does.
- Location. Warehousing real estate goes for a premium these days. It’s increasingly tougher to find/build warehouse property in key markets for reasonable costs. Warehouse location is a key consideration when you’re looking to optimize distribution and find reliable workers. 3PL public warehouse providers are often already established – and right where you need them.
- Flexibility. Markets fluctuate all the time. Public warehousing allows for flexibility during ebb-and-flow cycles. Easy scalability means greater cost efficiency when companies aren’t paying for space they don’t use.
- Add-on services. Things like kitting, packing, assembling, labeling – these are services that many public warehouses offer.
If you have questions about whether our Cleveland public warehousing facilities can meet your needs, contact us for a consultation.
For information on Northeast Ohio Warehousing, Inventory Management, and Trucking Services in Cleveland, Contact On Time Delivery & Warehouse by calling (440) 826-4630 or send us an email.
Additional Resources:
US warehousing demand shifting inland: JLL, Aug. 16, 2022, By William B. Cassidy, Journal of Commerce Online
More Blog Entries:
Tips for Choosing an Ohio Warehouse, Oct. 27, 2022, Northeast Ohio Public Warehousing Blog
Tips for Choosing an Ohio Warehouse
Warehousing is a crucial link in your supply chain network – in both global and domestic markets. Choosing the right Ohio warehouse for your operational needs can make a sizable difference in your firm’s ability to be efficient, effective, and profitable.
With Ohio warehouse space and labor at a premium, outsourcing often makes sense – especially if you can find a place that also provides services like packaging, repackaging, kitting, labeling, and distribution. Bonus if it’s near an airport.
When warehousing is done correctly, it provides numerous benefits beyond basic storage. Some of those include:
- Facilitates increased turnover.
- Improves production.
- Decreases shrinkage.
- Maximizes customer satisfaction with fewer products damaged in transit.
- Optimizes safety for workers and your goods.
Still, there is no denying warehousing costs have risen markedly in recent years. That’s thanks in large part to soaring e-commerce demand, which has expanded nearly 30 percent in the last three years. Even despite some predicted slowdowns on the horizon, the pandemic revealed that consumer consumption can be fairly resilient to economic cycles. Warehousing rent has climbed 3 percent a quarter nationally since 2020, reaching nearly $9.56/square foot earlier this year, according to The New York Times. (In some markets, it’s more than $15/square foot.)
If you’re looking for an Ohio warehouse that delivers great value for the cost, here are some priorities you’ll want to bear in mind to ensure you find the right fit.
- Location and accessibility to major linkages. Identify what mode – or modes – of transport is best-suited for your company’s operations. The warehouse that’s right for you will have easy access to that transport mode. For example, if air transport is one of the most efficient means of getting your goods from Point A to Point B, you will ideally find an Ohio warehouse that is within 20 miles or less of a major airport. (On Time Delivery & Warehouse, for instance, is just 4 miles from Cleveland Hopkins International Airport.) You also want to identify where your customers are primarily located. Warehousing that is close to your customer base can give you the advantage of more timely, cost-effective deliveries. Finally, an accessible warehouse that offers easy highway connectivity and few traffic backups so that trucks don’t waste time idling and goods get where they need to go as efficiently as possible.
- Diversity of capabilities. An Ohio warehouse with a broad range of capabilities is going to offer a better deal than those that offer storage and nothing else. If you can get integrated solutions for things like logistics planning, kitting, packaging and repackaging, labeling and sorting, CFS Freight, and distribution, it helps your firm come out ahead. Asset-based warehouse solutions – those that invest not only in the facility but in a transportation fleet and skilled workers – can offer a higher level of warehousing service.
- Experience. With new warehouses in Northeast Ohio cropping up daily, it’s a good idea to consider the experience of the provider. Newer facilities may offer some advantages, but take a look also at the operational dates. Supply chain logistics has always been a dynamic, evolving industry. Warehouse providers that have been around a while have the advantage of invaluable insights that have allowed them to stand the test of time.
- Material handling capacities. The warehouse you choose needs to have the availability of staging capacities and handling equipment that matches your demands. What kind of docks are you going to need? Will you need a facility with cross-docking capabilities? CFS? Last-mile delivery services? All this will help you determine which of your warehousing options will best suit your needs.
- Technology. Advancing technology has fundamentally altered the way warehouses operate – from electronic data exchanges to pick-by-vision systems to real-time product tracking. Keeping customers happy means providing them not only with faster results, but transparency through the process. Technology has been vital to that. Make sure the warehousing company you choose has the systems in place that will allow you to best serve your client base.
- Minimized risks. Handling, storing, and shipping products is not without risk. You want a warehousing management team that is fully aware of those risks, takes them seriously, values their team members’ safety, has appropriate safety measures in place, and invests in adequate insurance in case something does go wrong.
- Taxes and rates. Of course, cost needs to be considered. Compare each facility’s rental rate per-square-foot against the value they’re providing. Depending on your operation type, there may also be certain state or regional tax implications or incentives to weigh.
At On Time Delivery & Warehouse, we recognize that warehousing is an integral part of your operations – and we take our role in that seriously. Our goal is to help our clients maximize efficiency, excel, and ensure their own customers are fully satisfied with services that deliver their goods intact, on time, every time.
For information on Northeast Ohio Warehousing, Inventory Management, and Trucking Services in Cleveland, Contact On Time Delivery & Warehouse by calling (440) 826-4630 or send us an email.
Additional Resources:
Industrial Facilities Near Airports Command Rent Premiums, Oct. 5, 2022, CBRE
More Blog Entries:
6 Supply Chain Insights From Northeast Ohio Third-Party Logistics Warehouse Pros, Aug. 28, 2022, Cleveland, Ohio Warehousing Blog
Cleveland Transloading Service Benefits
When it comes to the shipping & logistics, moving goods from one destination to another, Cleveland transloading is a standout service that delivers value and results.
Transloading is a service that involves the transfer of goods from one mode of transportation to another along a designated shipping route. Most often, transloading involves full cargo containers shipped as ocean freight received at a port of entry. The goods are then processed and transferred to a different mode of delivery – usually trucking, rail, or barge – with products often palletized.
Transloading can also involve truck-to-truck and train-to-train exchanges. This is what often gets transloading confused with cross-docking. Cross-docking involves moving an intact pallet (or pallets) from one truck to another. Transloading, meanwhile, involves sorting and re-palletizing items and then transloading them to rail, air, or truck. Cross-docking can reduce or eliminate storage time and often involves quick turnaround times that are ideal for businesses operating on a deadline. Transloading can also deliver cost-savings, flexibility, and faster shipping.
Determining whether Cleveland transloading services are ideal for your situation involves weighing numerous factors. Our dedicated team of Northeast Ohio logistics professionals can help you identify the optimal solution for your operation.
Companies that avail themselves of strategic Cleveland transloading services keep their freight moving efficiently while keeping costs in check.
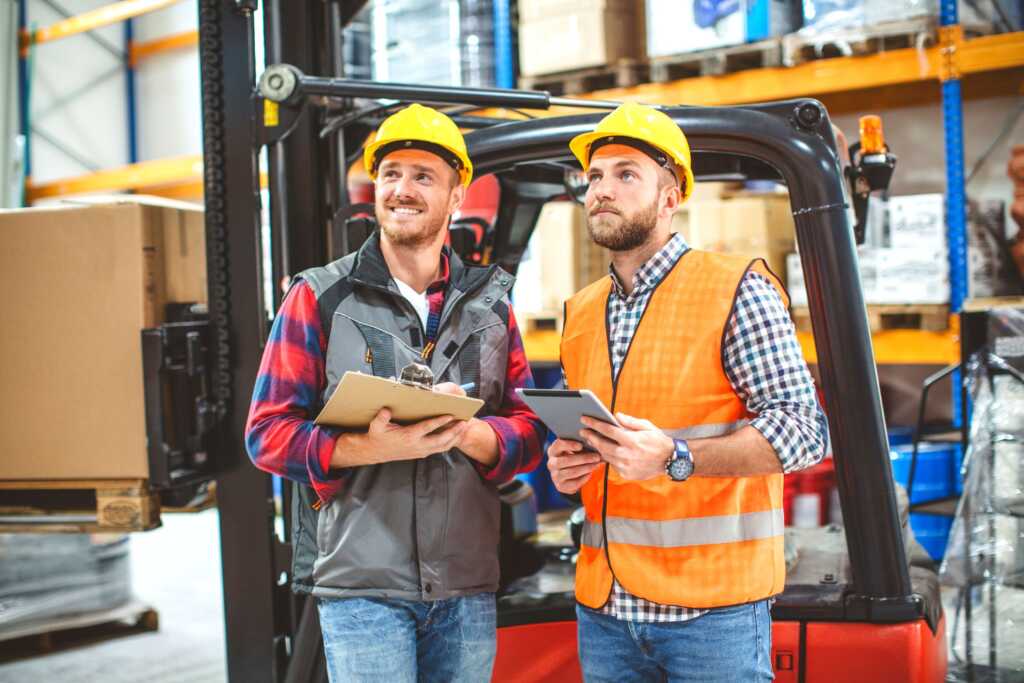
What Can Cleveland Transloading Do For You?
Transloading has become increasingly popular as e-commerce and international trade becomes the norm. Long-haul shipments often mean numerous shipping companies and transit modes. Transloading can help simplify complicated logistics and save businesses money.
Among the many advantages of transloading:
- Lower costs. Transloading is a great way to reduce your costs, particularly when you’re importing ocean container goods. Shippers can save big – usually in one of two ways. The first involves moving the contents of three, 40-foot containers into two, 53-foot trailers or domestic containers. You have the ability to select the transport mode through different legs of the journey that is going to be the most cost- and energy-efficient. Secondly, when you transload at the port, you avoid the need to use ocean containers to ship items inland. Steamships put a premium on maritime freight containers, so this is a major cost savings. (Bonus: A shipping container that is returned to more quickly to circulation means faster turnaround time on the next shipment, reducing bottlenecks and allowing for more efficient supply chains overall.)
- Faster transit times. It’s true that transloading takes a bit of time, usually about 1-3 days. However, by having the flexibility of several different transport mode options, you have the option of identifying the fastest option.
- More destination options within reach. Because transloading offers the option to choose any combination of freight transportation to best reach a certain end point, your goods can reach just about any destination.
- Simplified operations. Any bulk or heavy material shipping is going to pose some challenges. Transloading consolidates your shipments, and makes them easier – and cheaper – to transport.
- Promotes business growth. By allowing companies to hold down costs while reaching new markets and decentralizing your supply chain, transloading offers more opportunities to keep the customers they have – and attract new ones.
If you are considering transloading for your operation, our Cleveland team is prepared to offer detailed answers to your questions and provide a quote.
For information on our Transloading in Cleveland, Contact On Time Delivery & Warehouse by calling (440) 826-4630 or send us an email.
Additional Resources:
Transloading, by Will Kenton & Amanda Jackson, Jan. 31, 2021, Investopedia
More Blog Entries:
Cleveland Warehousing Helps Businesses Optimize Resources, Maximize Profits, July 30, 2022, Northeast Ohio Warehousing & Trucking Blog
- Categorized: 3PL, Freight Shipping, Trucking, Warehousing
- Tagged: Cleveland transloading, Cleveland transloading services, transloading Cleveland
Cleveland Trucking Carriers Steeled Operations for Potential Rail Strike
The threat of a potential U.S. freight train rail strike had Cleveland trucking carriers steeling their fleet and operations to help absorb at least some of the would-be mammouth impact. A last-minute tentative agreement struck with the intervention of the U.S. Department of Labor may have offset the immediate threat, but the whole ordeal underscores just how vital trucking services can be when other elements of intermodal transportation are jeopardized.
The New York Times reported tens of thousands of rail workers had threatened to strike in pursuit of better working conditions. Such action would have a catastrophic impact on supply chains across a vast range of industries throughout the U.S.
Rail moves an estimated two-fifths of long-distance U.S. freight and one-third of exports. The stakes of a potential shut down were very high – particularly as there isn’t a ton of slack in the trucking sector. If you are an organization that relies on the timely movement of goods across the country or the globe, this close call underscores the importance of securing a third-party logistics partner with strong connections to reliable Cleveland trucking carriers who can help arrange alternative transport and delivery methods in the face of unexpected hurdles. And let’s face: Unexpected hurdles of all stripes are almost a given with global supply chains.
A rail strike and increased reliance on Cleveland trucking carriers would mean substantial delays and higher costs. But it’s worth noting that truckers are already responsible for carrying nearly three-fourths of the nation’s goods as it is.
If all of America’s 7,000 long-distance daily freight trains were brought to a halt, the American Trucking Associations estimates it would require some 460,000 additional long-haul trucks daily to meet the current demand. Although there is no longer a trucking shortage, there isn’t much of a surplus either.
As our Cleveland trucking carriers can explain, rail is a central component of our complex global supply chains, which rely on the carefully-coordinated movements of cargo ships, freight trains, and trucks. This is known as intermodal transportation, and it helps to effectively eases the movement of goods across air, sea, and land. Compromise one of those links in the supply chain, and there will be a near-immediate domino effect to the system – one that has already been under significant strain since the pandemic.
Still, rail is generally recognized as the weakest of the three intermodal supply chain links. It is less flexible in responding to demand surges and bottlenecks. Over the last five years, as carriers have sought to limit service to lower costs as part of a strategy known as Precision Scheduled Railroading, nearly a quarter of rail worker jobs have been slashed. Rail companies say the reconfiguration has been an effort to become more agile and responsive to supply chain demands and challenges.
There are 12 railroad unions that form the National Freight Rail Bargaining. This coalition uses its combined power to push for employee labor demands. The most recent disputes concerned matters like higher pay, better working conditions, more paid time off, and schedules that are more flexible. (Attendance policies in particular have been a huge point of contention.)
There hasn’t been a U.S. railroad strike 30 years – and the impacts of that one in 1992 were immediate and serious. It took only three days before Congress intervened and a new contract was brokered.
Negotiations for the current rail worker contract have been ongoing for three years. Recognizing the potential harm this might do, the White House and U.S. Labor Secretary stepped in, brokering a tentative agreement. However, it’s still not officially finalized, meaning our Cleveland trucking carriers are still gearing up for the possibility the deal could fall through. The new contract won’t become final until members review the terms and approve it with a ratification vote.
Still, companies might still want to prepare for setbacks just in case. Some retailers are already diverting Asian goods that typically come through West Coast ports to those on the East Coast, at places like Newark, Savannah, and Charleston. Cleveland trucking carriers’ routes frequently take them to-and-fro at these ports. The added demand could mean an uptick in trucking rates, but worth it for many organizations if it means their goods arrive in tact and on time.
If a rail strike were to still happen now or in the coming months, our Cleveland trucking and logistics experts opine it probably wouldn’t last long. Too many industries are too deeply invested, and the pressure to resolve matters quickly would be enormous. The government’s heavy-handed involvement at the final hour is further evidence of that. But even a short-lived strike could have wide ripple effects, so companies would do well to plan for that possibility.
If you are a Northeast Ohio firm that relies heavily on rail transport to move your import/export goods, diversifying your mode of transport and collaborating with a third-party logistics firm with trucking capabilities may improve the overall security of your supply chain.
For information on Trucking, 3PL, and Warehousing Services in Cleveland, Contact On Time Delivery & Warehouse by calling (440) 826-4630 or send us an email.
Additional Resources:
More Blog Entries:
Seasonal Cycles of Ohio Trucking Are Back, Per Cleveland Trucking Experts, July 20, 2022, Cleveland Trucking Blog
- Categorized: Company News