Blog
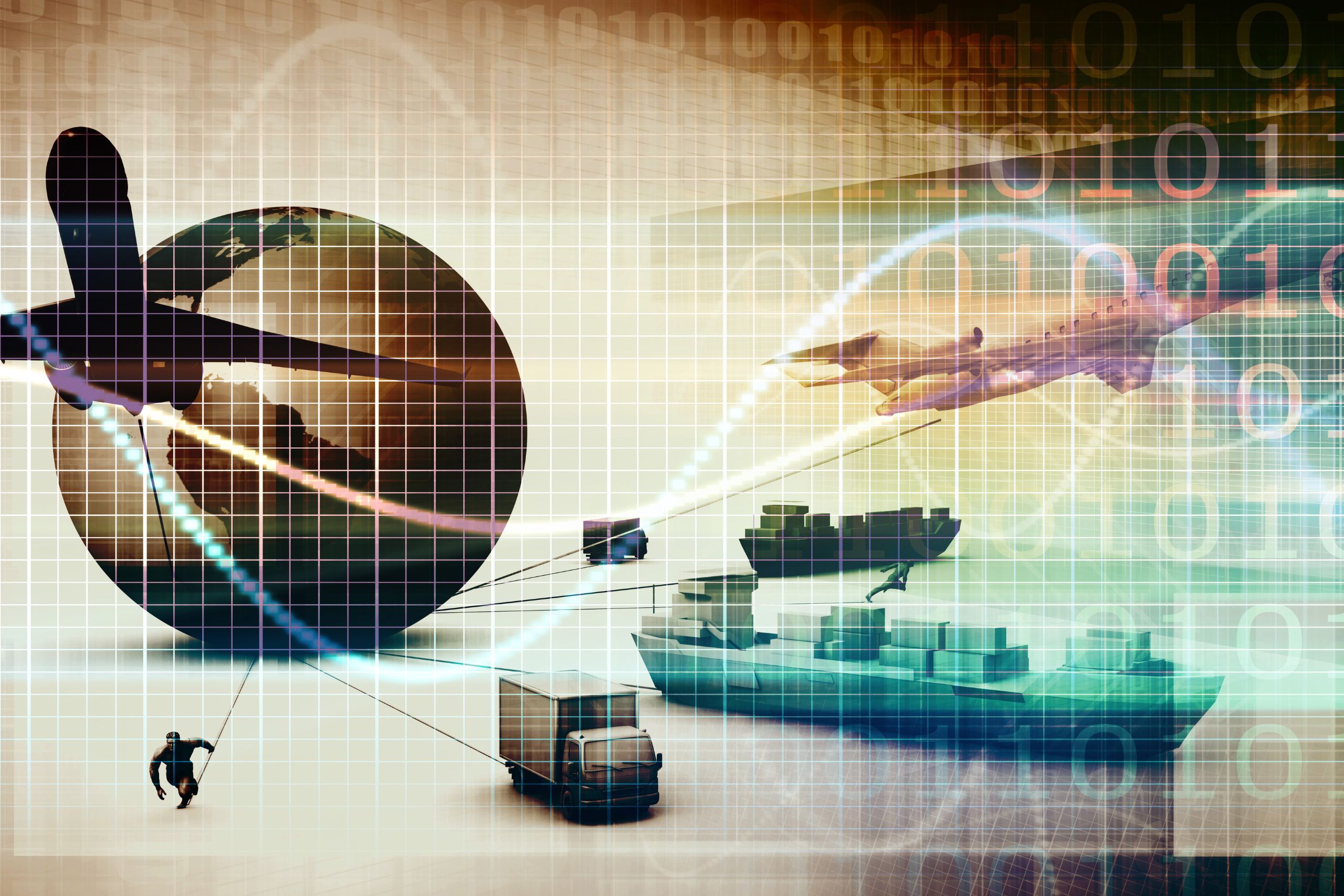
6 Supply Chain Insights From Northeast Ohio Third-Party Logistics Warehouse Pros
As Northeast Ohio third-party logistics warehouse professionals, we understand the complexities of supply chain management better than anyone. Increasingly, it’s important that our clients have a grasp of them as well.
In recent years, the volatility of local and global supply chains has been on full display not only to manufacturers and distributors but consumers as well. There is a growing expectation that savvy businesses will take measures not just to respond to supply chain hiccups when they arise, but to become better at predicting and preparing for their inevitability.
Working with an Ohio third-party logistics team helps your company to do that. It also provides consumers with broader transparency and more responsive communication when problems occur.
With this in mind, the Ohio 3PL team at On Time Delivery & Warehouse offers the following list of basic supply chain insights.
Modern supply chains are increasingly complex.
Most supply chains can be broken down into two basic segments: Production and distribution. But that’s really where the simplicity ends.
Consider, for instance, a basic laptop computer. It can easily have 3,000 different parts. Your typical Ford truck? It’s likely to have at least 30,000 components. An effective supply chain is going to have numerous layers of varying sophistication, typically involving specialists who can supply certain components. Often, businesses end up with many layers of supply chains – and it can get even murkier when your suppliers don’t want you to know who their suppliers are, for fear you’ll just go around them if possible. This can be especially problematic if a lower-tier supply shuts down – and you aren’t even made aware of it until a certain time period. That can eventually lead to major supply chain snarls – which is precisely what we saw during the pandemic.
On the distribution end of things, issues with congested ports and labor shortages have resulted in bottlenecks. Working with an Ohio third-party logistics company helps ensure you if something falls through, you have alternative routes and means (by road, air, and sea).
Unexpected Demand May Not Mean What You Think.
Customers signal their demand by making purchases. This prompts businesses to ramp up supply. But this sort of demand forecasting can cause problems if spikes are interpreted as fundamental shifts in demand.
We saw this during COVID-19 when it came to things like exercise bikes. There were huge customer demands, retailers flooded their suppliers with orders, suppliers started cranking up production and returned the flow back to retailers – who by then realized they had too much and cut back substantially on future orders. This lead to major supply chain headaches – manufacturers cut production, suppliers were left with an overstock of raw materials and customers were left cooling their heels for extended periods waiting for deliveries.
When it comes to sudden demand spikes, it’s best to proceed with a degree of caution.
Just-In-Time Production Can Be a Practical Solution.
To avoid the whiplash of sudden demand spikes that just as suddenly fall, some companies have found just-in-time production a practical solution. As our Ohio third-party logistics pros can explain, just-in-time production involves making precisely what you need – and only when you need it. The idea is you’re only carrying as much inventory as you need, raw materials get delivered only just in time. If there is an issue with any of those parts/raw materials, the impact is typically minimal because the orders are smaller.
However, this solution really only makes sense when suppliers, manufacturers, and distributors are relatively close and/or when the supply chains are fairly lean. If your network is more global, trying to work out exactly when you’re going to need a delivery – and how much it will be – can be tricky. It can lead to problems when you factor in demand spikes and supply chain bottlenecks (particularly those involving international shipments, which can get held up for weeks on end).
Just-in-time production can work for some companies, but it’s wise to consult with your 3PL to see whether your supply chain has any weak links that can be tightened first.
The Bigger Your Supply Chain, the More Opportunities for Disruption.
Many companies rely on lengthy distribution chains. For example, if you’re shipping furniture from a factory in Sweden to a store in Northeast Ohio, you might need an air leg, an ocean leg, a rail leg, and truck transfers. The more links your supply chain has, the riskier it may be, particularly when each link directly depends on the smooth function of all the others. Keep in mind too – some of those links depend on cogs and sprockets that are on different tracks entirely.
Longer logistics threads are more vulnerable to delays than shorter ones. When you work with a third-party logistics partner, you have the benefit not only of transparency and seeing potential issues just before or immediately after they arise, but also alternatives when that happens.
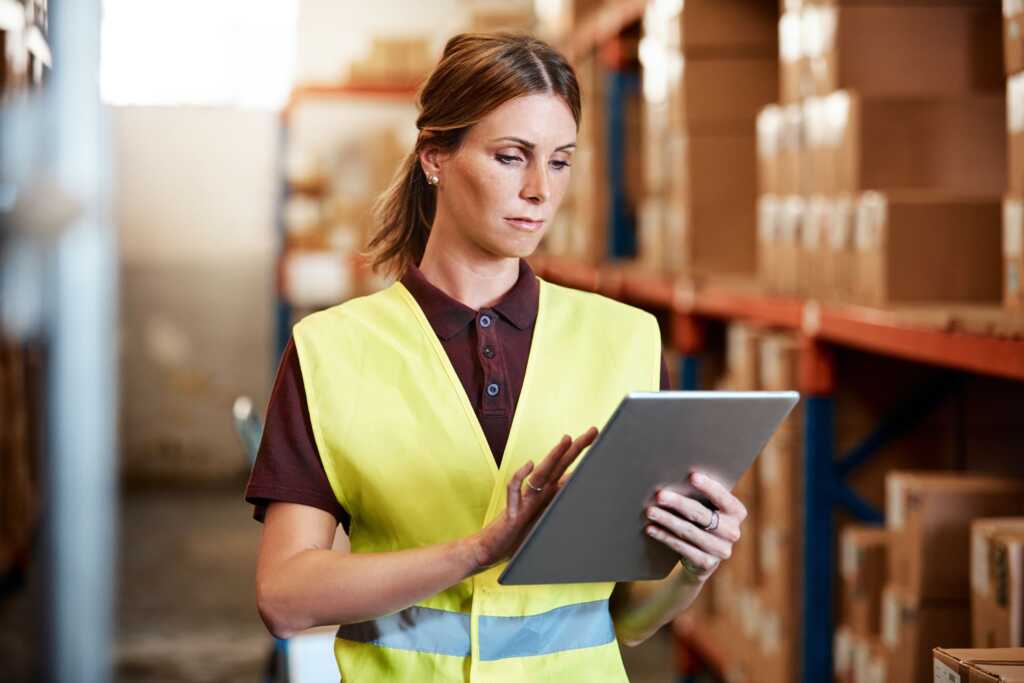
Ordering More Than Necessary May Exacerbate Shortages.
Ideally, companies are only going to order as much of an item as they think they are going to consume or sell until the following cycle. However, if you forecast that a certain product may become particularly in-demand, it may seem smart to order extra.
However, where this is a problem is that some companies might start ordering double or triple what they actually need. This not only leads to shortages in the immediate, but can result in companies having far too much inventory – which inevitably leads to the need for more warehouse space, etc. You may end up with further losses if you’re forced to slash prices to just to offload it.
It can be tough to determine the exact right amount of just-in-case product to keep on hand. It’s a balancing act. Working with a dedicated Ohio third-party logistics team can help ensure both communication and supply chain visibility so that you can accurately forecast just how much you’re going to need.
Ohio Third-Party Logistics Partner Can Help Reduce Bottlenecks By Providing Big Picture Snapshots.
Bottlenecks in the supply chain are commonly the result of a lack of visibility – both for what’s in the pipeline on its way to you and then what comes after.
For example, it’s easy to see hundreds of ships stalled at a port and conclude, “Clearly, lack of efficiency at the port is the problem.” In reality, the actual issue might be that there was poor communication among downstream distribution centers. You could increase the port’s capacity 200 percent by keeping it open 24-7, but it’s not going to make much difference in the backlog if there is no one to pick up those goods or nowhere for it to immediately go.
Working with a team of skilled, experienced 3PL professionals can help provide a big picture lens, allowing you to identify potential issues before they become a major problem – easing the flow of goods downstream all the way to your customers.
If you have questions about how our Northeast Ohio third-party logistics warehousing & trucking team can help improve your supply chain visibility and flow, we’re here to provide further insight.
For information on 3PL Warehousing, Inventory Management, and Trucking Services in Cleveland, Contact On Time Delivery & Warehouse by calling (440) 826-4630 or send us an email.
Additional Resources:
Supply Chain Pressures Ebbed in July, Aug. 15, 2022, Central Banks Research, The Wall Street Journal
More Blog Entries:
Cleveland 3PL Recommends Ample Planning to Cope With Packaging Shortage, June 28, 2022, Northeast Ohio Warehousing News Blog
- Categorized: 3PL, Warehousing
- Tagged: Cleveland 3PL, Cleveland logistics company, Cleveland Ohio third-party logistics, Cleveland supply chain experts, Cleveland supply chain partners, Cleveland warehousing, Northeast Ohio 3PL, Northeast Ohio logistics, Northeast Ohio third-party logistics, Ohio logistics, Ohio third-party logistics
Comments are closed.