Cross Dock Warehouse
Cross Dock Warehouse
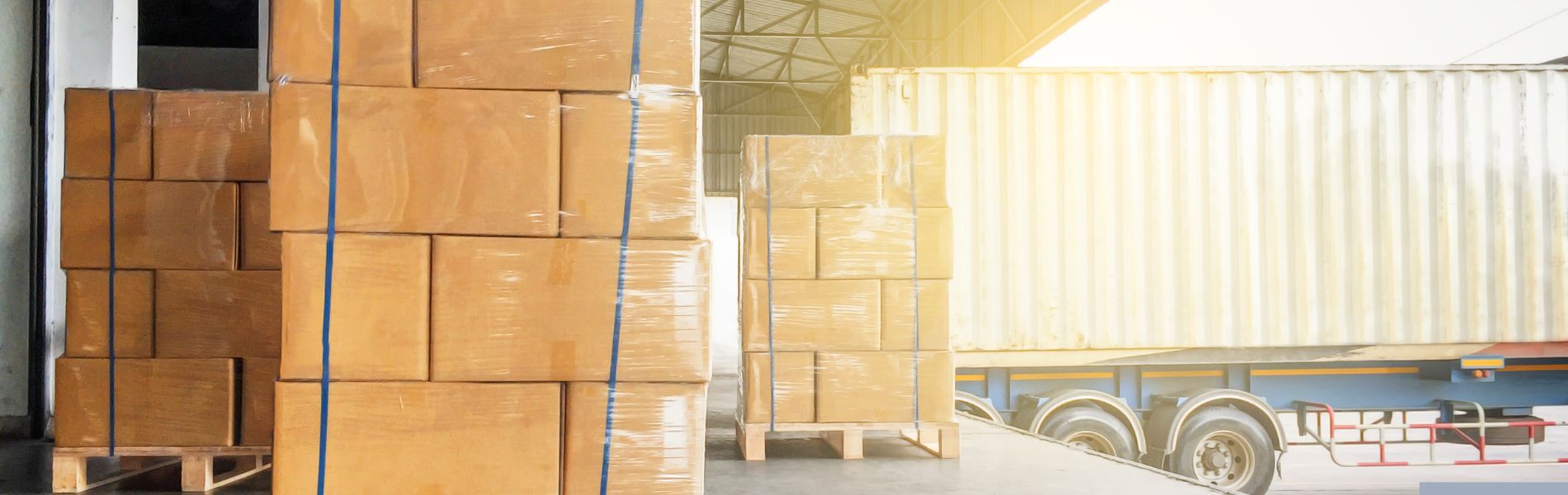
A Cleveland cross dock warehouse can save your business considerable time and money while speeding up shipments and boosting brand loyalty.
Cross docking is a logistics strategy that requires a fair amount of coordination between supply chain partners, but it ultimately limits the length of storage, optimizes inventory control, consolidates similar shipments and reduces transportation and labor costs.
For most companies, about 30% of overall product sale costs are dedicated to distribution. Cross docking optimizes the distribution process. A robust cross-docking strategy can make a major difference in overhead expenses - particularly when companies leverage the resources of an established 3PL equipped to immediately facilitate faster turnaround times.
The less time products sit on warehouse shelves, the less risk of damage, spoilage or obsolescence. Quicker deliveries also keep customers happier.
What is Cross-Docking?
Cross-dock warehousing is when goods are transferred from inbound transportation to outbound transportation – with little to no storage in between.
Essentially, a cross dock warehouse serves as more of a sorting center rather than storage facility, ensuring goods move quickly through the chain of supply. More often than not, goods will spend less than 24 hours at the warehouse.
Although there’s bound to be variation between facilities and shipment types, the basic step-by-step breakdown for a crossdock warehouse is:
- Receiving. Inbound shipments arrive at the cross dock facility.
- Sorting. Goods are scheduled for quick sorting and consolidation, usually grouped on the basis of their type or destination.
- Transferring. Sorted goods get moved to the outbound dock.
- Shipping. Outbound shipments are loaded up before being dispatched to their final destination.
This can happen pre-distribution (with products sorted and packed based on customer orders prior to arrival at the warehouse) and/or post-distribution (with shipments sorted and packed at the warehouse based on customer demand).
As noted in research published in the journal Sustainability, cross docking reduces:
- Delivery lead time from suppliers & customers.
- Storage space requirements and the risk of product damage/obsolescence caused by long-term storage.
- Overstock, which improves resource utilization and energy efficiency.
It also improves control over delivery schedules as well as the level of customer service.
The catch is cross docking takes a lot of logistical coordination and supply chain visibility to do well. Most companies don’t have that kind of capability in-house. By partnering with an established Cleveland cross dock warehouse, customers can sidestep the sizable learning curve and investment needed to get it right.
Origins of Cross Dock Warehousing
Cross-docking got its start back in the early 1900s. However, it didn’t truly gain sufficient traction until the 1980s. That’s when the economy saw a major expansion of just-in-time (JIT) manufacturing.
JIT manufacturing involves a production schedule where goods are created to meet demand – not with intent to create an advance surplus to meet future demand. This reduced costs and sped up delivery, but also necessitated greater supply chain efficiency.
Retail giants were the first on the cross dock warehouse scene, favoring the streamlined distribution and reduced inventory holding and order picking costs. Wal-Mart, for example, was using cross-docking for about 85% of its inventory by the early 1990s, contributing to reported cost savings of about 2-3%.
Recognition of those benefits has continued to grow - especially in recent years with the rise of e-commerce. It’s leveraged by car manufacturers, farmers and grocers, pharmaceutical companies, online retailers and more.
Cleveland Cross Dock Warehouse Options
For all its upsides, cross docking is not a practice entirely without pitfalls.
It can be risky because products aren’t stored int between the time they’re moved from incoming to outgoing trucks. That can increase the possibility of product damage if there isn’t careful coordination with partners who are both timely and reliable.
Cross docking is impossible to pull off without extensive preparation. It requires careful planning using in-depth operational insights across sizable transport carrier networks and advanced tech to initiate and maintain real-time tracking.
Operations launching a cross dock warehouse in-house must devote a sizable upfront investment. They should also be prepared for the occasional costly misstep while navigating the broad learning curve.
Alternatively, companies can outsource to a 3PL Cleveland warehouse with turnkey cross docking services. But before you sign a contract, it’s important to get a sense of exactly what kind of cross docking services you want.
Possibilities include:
- Continuous cross docking. Often the fastest method, continuous cross-docking involves one centralized site from which goods in incoming shipments are transferred to outbound trucks. Careful planning is critical to ensure the seamless flow of inbound and outbound trucks.
- Consolidation arrangements. Customers with smaller product loads can save money by having their shipments consolidated with other smaller shipments – paying less-than-truckload rates while still getting goods delivered quickly.
- Deconsolidation arrangements. Clients with larger loads contract to have those broken down to make local, customer-direct transport easier.
If you aren’t sure whether cross docking makes sense for your business or what type of cross docking you need, our logistics experts can spell out your options and zero in on the strategy that makes the most sense.
Need more information about our Cleveland cross dock warehouse services? Contact us today!